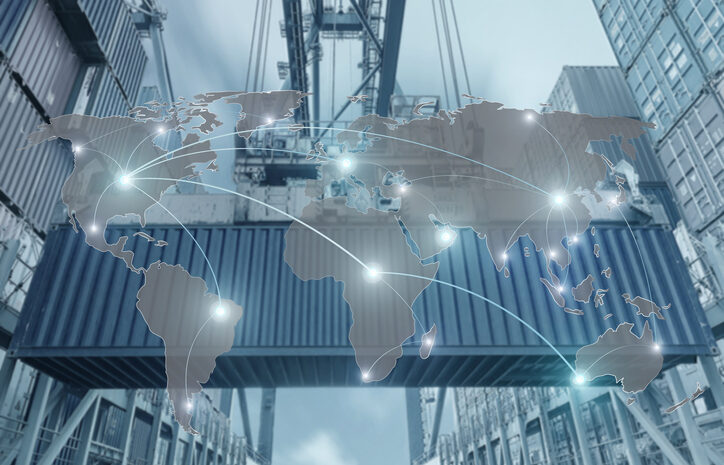
Case Study: Successful Supply Chain Management in a Large-Scale Commercial Project
Driver shortages, Labor shortages. Extreme weather. Unavoidable world events. These are just a few of the major challenges facing commercial construction organizations everywhere as they relate to the current status of the global supply chain.
Equally complicating things for large-scale commercial projects specifically is the rising cost of raw materials. According to one recent study, the amount of physical inventory on-hand is actually about 20% below pre-pandemic levels as of 2023. Despite that, the cost of those materials are 12% higher over the same period. So not only are raw materials more difficult to get, they’re also appreciably more expensive.
That’s a big part of the reason why an emphasis on supply chain management is of paramount importance. Just because a project is larger in scale (and presumably has a larger budget) doesn’t mean it can be forced to deal with delays, cost overruns, and similar issues. Recently, one successful commercial construction company re-thought their approach to supply chain management ahead of an upcoming project. The approach was definitely something a lot of similar organizations can learn from moving forward.
Reassessing the “Old School” Approach to Supply Chain Management
In past large-scale commercial projects, the company in question had run up against unexpected delays for a number of reasons. Perhaps the biggest was that raw materials had to travel A) large distances, across B) many steps. Each step introduced another potential point of failure for the process.
This inspired them to take a look at simplifying their process as much as possible. They began relationships with vendors that allowed them to locally source raw materials whenever possible. Yes, it’s true that they paid a bit of additional money upfront – but they also virtually eliminated those delays in a way that helped them control costs across the entirety of the project. Energy, freight, and labor were no longer as big of a risk factor as they once were, despite the fact that all of these things were increasing across the globe.
Another step that the construction company in question took to meaningfully improve their supply chain management had to do with overhauling their data management process.
Again, we’ve entered into an era when supply chains are becoming increasingly larger and more complex all the time. Because of this, sharing data in an efficient and secure manner with vendors and other partners is paramount.
Sharing freight price and availability data, for example, can help people make better choices in terms of when and where to ship in order to avoid surging prices. If nothing else, it will allow them to better handle the rising cost of energy. The same data sharing methods can also be an opportunity to make demand forecasting easier. The more visibility you have into the supply chain, the more actionable information you can see about things like global disruption.
The more data you can draw from, the easier it is to analyze the true situation. This allows you (and your partners) to properly estimate demand, which you can then react to accordingly. You’re not acting based on gut instinct or intuition. You’re making decisions based on fact, as it should be.
A Better Path Forward Begins With Supply Chain Management
Overall, this is just one example of an organization that learned the myriad of different benefits that supply chain management brings with it. In the short-term, the construction company was able to significantly increase efficiency – cutting costs without sacrificing quality for the large-scale commercial project they were working on. This helped them minimize risk in an inherently competitive climate.
Over the long-term, a more thoughtful approach to supply chain management will also allow them to deliver superior results while coming in on-time and on-budget. This will definitely lead to increased customer satisfaction. This will lead to increased revenue and ultimately better cash flow.
Again – any one of these benefits, if achieved in a vacuum, would be enough for most construction company leaders to rethink the “old school” approach to supply chain management that they’re likely still relying on. When you consider that you get all of them at once, all by way of a process that can be easily recreated across large-scale commercial projects in the future, you’re looking at a perfect storm in the best possible way.
To find out more information about how to fortify your supply chain management efforts within the context of a large-scale commercial project, or to speak to someone about your upcoming project in a bit more detail, please feel free to contact the team at Level X Supply today.
Commercial Construction Supplies
Clearly, if you’re looking to streamline your supply chain and keep your projects on track, you can benefit significantly from working with a virtual warehouse. To learn more from the premier commercial construction supply company, contact LevelXSupply today.